LIQTRA is 3D Printing Success for Stakeholders Across Industries
LIQTRA provides innovative solutions tailored to a wide range of business needs. Our technology empowers companies to enhance efficiency, drive sustainability, and adapt to changing market demands. Explore our use cases to see how LIQTRA’s solutions are applied across various sectors, delivering real-world impact and measurable results. Whether you’re looking to streamline processes, optimize energy consumption, or elevate productivity, LIQTRA’s proven expertise can help you achieve your goals.
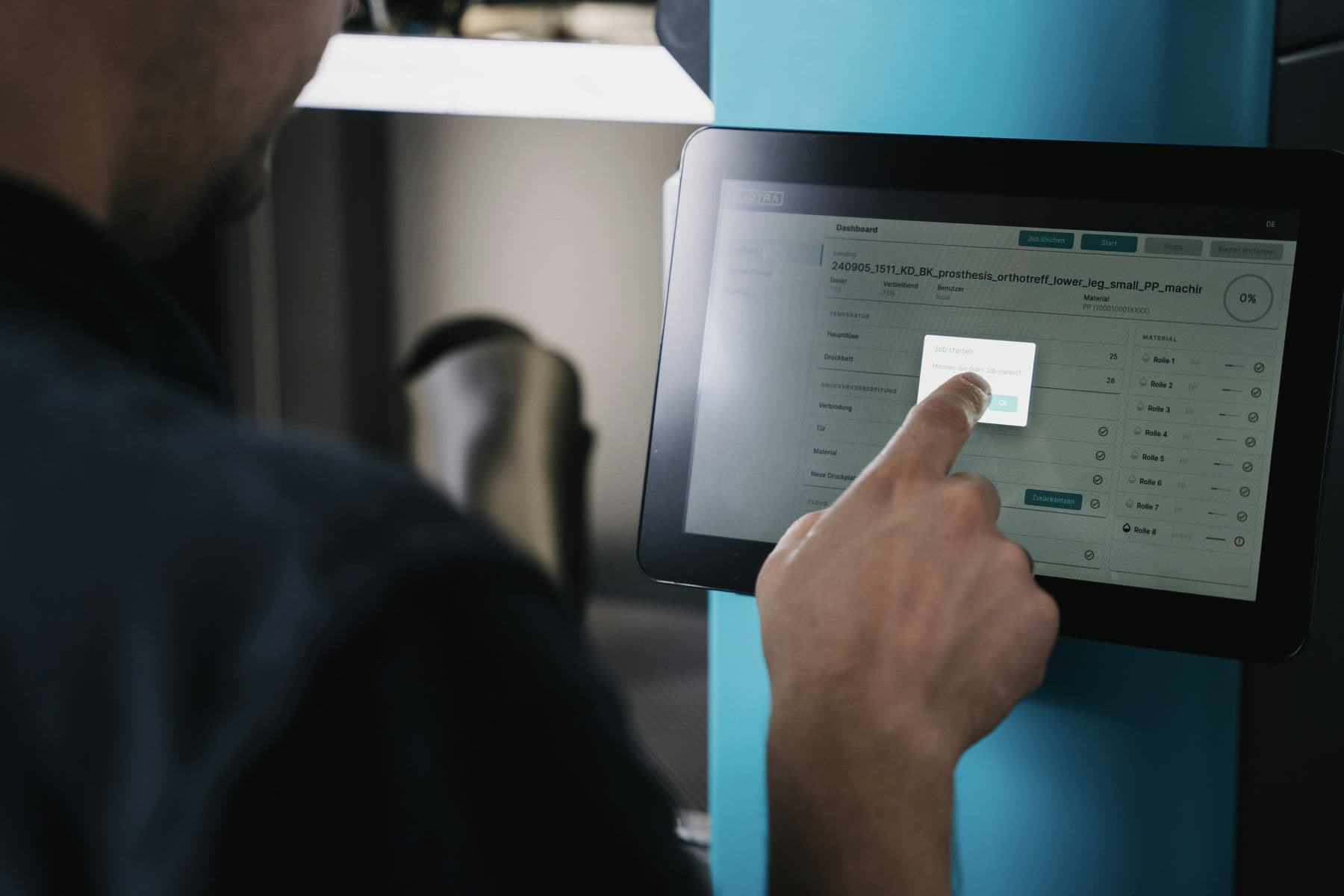
Prostheses for Acute Care
Fast 3D printing with multi-nozzle technology enables the production of prosthetic legs for acute care overnight.
After 3D printing has already been successfully used for the production of medical aids, such as orthoses or insoles, a market is now opening up through the production of individual leg prostheses. A fast production process is a prerequisite for fitting, acute care and replacement prostheses. While single nozzle 3D printing causes process times of over 24 hours, reduced process times of multi-nozzle technology enable overnight production. To achieve the maximum part quality, we cooperate with orthopedists and medical supply stores as development partners to cover the entire process chain from part design and material selection to process planning and 3D printing.
Results:
- 3D printing is competitive due to short process times
- Digital process chain for fast and comfortable patient care
- Use of certified filaments for skin contact
- Multi-material 3D printing allows further design freedom
On-Board Computer
Holistic product development – from the control board to the design and 3D printing of the functional housing.
The on-board computer solution MC move+ for local public transport consists of a computer tablet for the driver, a customer display, a ticket printer and a QR code scanner – all integrated into a 3D-printed housing. The power supply and communication between the individual components is realized via a custom PCB developed by LIQTRA. The entire project from the idea to customer deployment was completed in around 6 months, which shows the potential of 3D printing in terms of cost savings and avoiding long delivery times for tools.
Results:
- 3D printing minimizes development times
- Economic small series production of housings
- Reduction of housing parts due to integral design
- 3D printing enables decentralized spare part production
On-Board Computer
Holistic product development – from the control board to the design and 3D printing of the functional housing.
The on-board computer solution MC move+ for local public transport consists of a computer tablet for the driver, a customer display, a ticket printer and a QR code scanner – all integrated into a 3D-printed housing. The power supply and communication between the individual components is realized via a custom PCB developed by LIQTRA. The entire project from the idea to customer deployment was completed in around 6 months, which shows the potential of 3D printing in terms of cost savings and avoiding long delivery times for tools.
Results:
- 3D printing minimizes development times
- Economic small series production of housings
- Reduction of housing parts due to integral design
- 3D printing enables decentralized spare part production
Trial Leg Prosthetics
Short printing times enable the rapid production of trial prostheses to optimize the patient-individual shape.
By reducing the production time and cost associated with traditional prosthetic trials, LIQTRA empowers both practitioners and patients to make better-informed decisions with greater confidence. The use of PP ensures that these test prosthetics provide a realistic fit and function, allowing patients to experience and evaluate the prosthesis comfortably before committing to a final version. Whether used in clinics, hospitals, or rehabilitation centers, our approach to 3D printing trial prosthetics marks a significant advancement in personalized patient care, improving accessibility and setting new standards for the prosthetics industry.
Results:
- Easy localization of pressure points due to transparent material
- Digital process chain for fast and comfortable patient care
- Use of certified filaments for skin contact
- 3D printing is competitive due to short process times
Intercom System
Multi-material 3D printing allows new functional part designs by combining different materials in one 3D printing process.
Our focus in developing multi-material 3D printing is on offering different material properties for functional part designs, such as hard and strong parts with softer surfaces. In cooperation with our partner Sittig Technology we are currently working on the production of housings for intercom systems, in which conductive materials are combined with insulating materials, whereby ESD protection is integrated directly into the printed part.
Results:
- Economical production of small series intercom systems
- Usage of 3D printing enables decentralized spare part production
- Reduction of housing parts due to integral design
- Substitution of the inner metal shell leads to large weight savings
Intercom System
Multi-material 3D printing allows new functional part designs by combining different materials in one 3D printing process.
Our focus in developing multi-material 3D printing is on offering different material properties for functional part designs, such as hard and strong parts with softer surfaces. In cooperation with our partner Sittig Technology we are currently working on the production of housings for intercom systems, in which conductive materials are combined with insulating materials, whereby ESD protection is integrated directly into the printed part.
Results:
- Economical production of small series intercom systems
- Usage of 3D printing enables decentralized spare part production
- Reduction of housing parts due to integral design
- Substitution of the inner metal shell leads to large weight savings